2025 Autor: Howard Calhoun | [email protected]. Zadnja izmjena: 2025-01-24 13:13
Danas se od čelika pravi ogroman broj raznih stvari, dijelova itd. Naravno, za to je potrebna velika količina izvornog materijala. Stoga se u pogonima već dugo koristi metoda kontinuiranog livenja čelika, koju karakteriše najvažnija karakteristika - visoka produktivnost.
Osnovna oprema za rad
Do danas je poznato nekoliko instalacija za livenje čelika na ovaj način, a skraćeno su UNRS. U početku je razvijena i puštena u proizvodnju instalacija vertikalnog tipa, koja se nalazi 20-30 metara ispod nivoa poda radionice. Međutim, kasnije je želja da se napusti produbljivanje poda postala glavni motor za razvoj ovih instalacija. To je dovelo do razvoja i implementacije postrojenja za kontinuirano livenje u obliku tornja. Visina ovih instalacija bila je 40 m. Međutim, ova verzija mašine nije bila u širokoj upotrebi iz dva razloga. Prvo, izgraditetakva jedinica u radionici je prilično problematična i naporna. Drugo, pojavile su se još više poteškoća s njegovim radom.
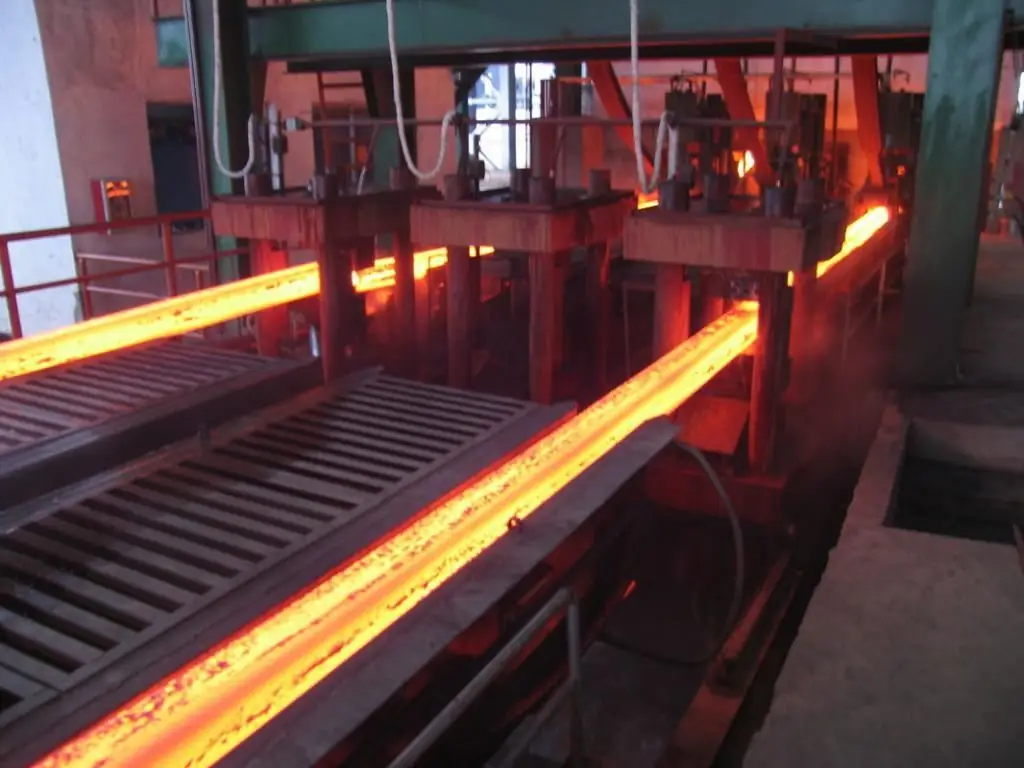
Zakrivljene i radijalne instalacije
Vremenom je kontinuirano livenje čelika prebačeno na rad sa mašinama za vertikalno savijanje. Glavna karakteristika je savijanje ingota koji izlazi nakon osovine za 90 stepeni. Nakon toga je u instalaciji korišćen poseban mehanizam za ispravljanje za ispravljanje ingota, a tek nakon ove faze je došlo do rezanja. Kontinuirano lijevanje čelika na takvoj opremi iz nekog razloga nije postalo jako popularno. Prvo, zavoj je, naravno, omogućio smanjenje visine, ali je istovremeno ozbiljno ograničio poprečni presjek samog ingota. Što je više bilo potrebno da se dobije presek materijala, savijanje je moralo biti veće, što znači da se visina ponovo povećava. Drugo, mašine za savijanje su postavljene u čeličane sa još većim poteškoćama nego vertikalne.
Danas, instalacije za kontinuirano livenje radijalnog čelika dobijaju sve veću popularnost. Na takvoj jedinici, ingot se formira u kalupu i napušta ga duž istog luka duž kojeg je ušao u njega. Nakon toga će se ispraviti mehanizmom za povlačenje i ispravljanje. I tada već možete početi rezati ingot u prazne dijelove. Upravo se ovaj dizajn u praksi pokazao najracionalnijim u organizaciji protoka robe u čeličani.
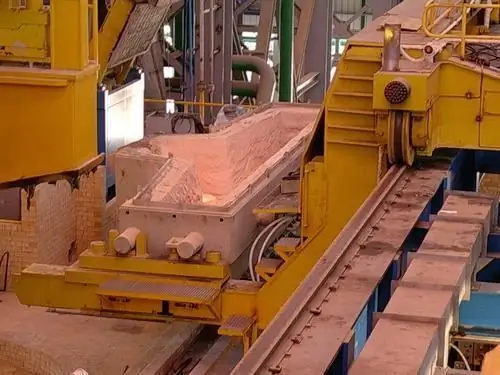
Gdje počinje kasting
Tehnologija kontinuiranoglivenje čelika je prilično komplikovan proces. Međutim, pošteno je reći da princip ostaje isti bez obzira na postavku proizvodnje koja se koristi. Možete razmotriti tehnologiju koristeći primjer vertikalnog UNRS-a.
Mašina se isporučuje sa kutlačom za izlivanje čelika kroz specijalnu dizalicu. Nakon toga čelik teče u lonac, koji ima čep. Za jednostruke mašine biće jedan čep, za mašine sa više lanaca biće jedan čep po struji. Osim toga, lonac ima posebnu pregradu za zadržavanje šljake. Čelik će teći u kalup, prolazeći kroz staklo za doziranje ili čep. Ovdje je važno napomenuti da se prije prvog livenja sjeme unosi u kalup sa donje strane. Ispunjava ili poprečni presjek cijelog kalupa, ili samo oblik radnog komada. Gornji sloj sjemena bit će dno kalupa. Osim toga, ima i oblik lastavičjeg repa za buduće spajanje ingotom.
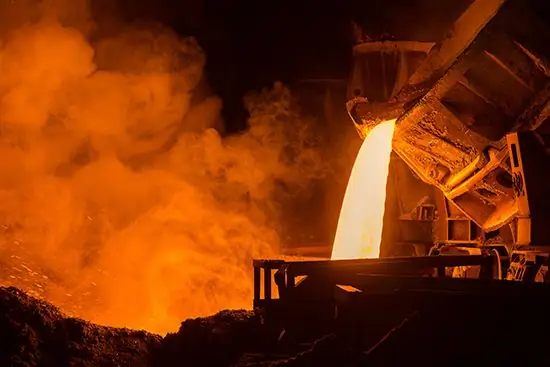
Dalje kasting
Dalje, u procesu kontinuiranog livenja čelika, potrebno je sačekati dok se nivo sirovine ne podigne iznad semena na visinu od oko 300-400 mm. Kada se to dogodi, pokreće se mehanizam koji pokreće uređaj za povlačenje. Ima vučne valjke pod čijim uticajem će sjeme pasti i sa sobom povući stvoreni ingot.
Mašina za kontinuirano livenje ima kalup obično napravljen od bakra sa šupljim zidovima. On je pod intenzivandjelovanjem rashladne vode, a njegov unutrašnji presjek odgovara obliku ingota koji se dobija. Ovdje se formira kora bez ingota. Pri velikim brzinama livenja može doći do kidanja ove kore i curenja metala. Da bi se ovo izbjeglo, kalup karakteriziraju povratni pokreti.
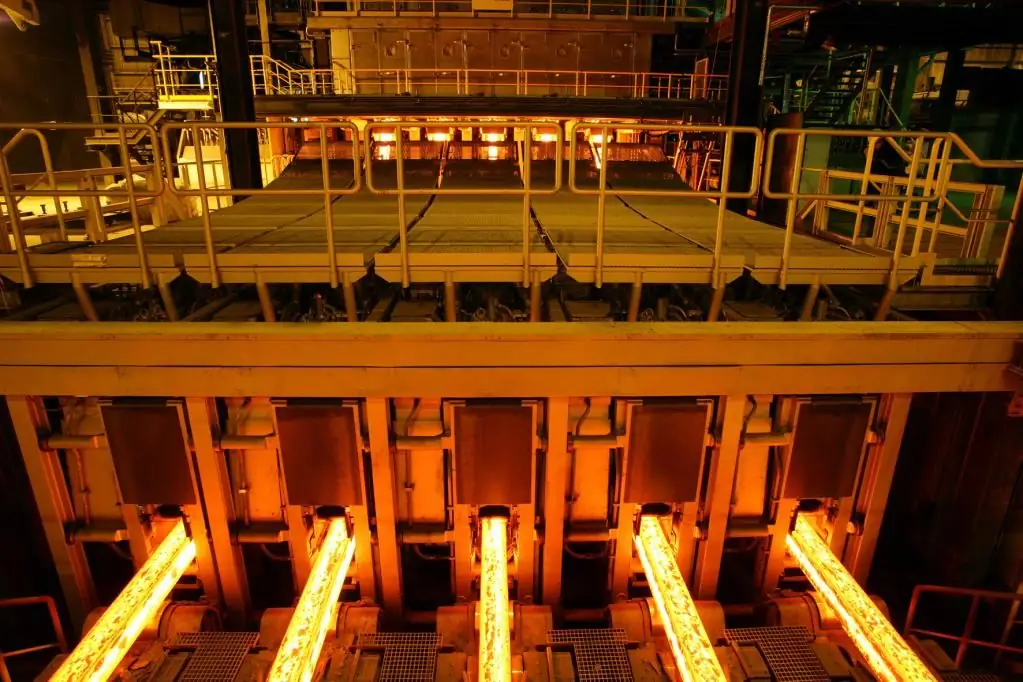
Karakteristike rada kalupa
Mašina za kontinuirano livenje ima električni motor odgovoran za stvaranje ovog povratnog kretanja. To se postiže snagom mjenjača s mehanizmom za okretanje bregastog tipa. Prvo, kalup se kreće u istom smjeru kao i radni komad, odnosno prema dolje, a nakon što je proces završen, vraća se natrag gore. Hod zamaha je od 10 do 40 mm. Kalup je važan pretinac u kontinuiranom livenju čelika na bilo kojoj vrsti opreme, te se stoga njegovi zidovi podmazuju parafinom ili bilo kojim drugim mazivom pogodnim za karakteristike.
Važno je napomenuti da se u modernoj opremi nivo metala kontroliše radiometrijski primenom kontrolnog signala na čep livačkog lonca. U samom kalupu se može stvoriti neutralna ili redukujuća atmosfera iznad nivoa metala kako bi se izbjegla oksidacija proizvoda tokom proizvodnje.
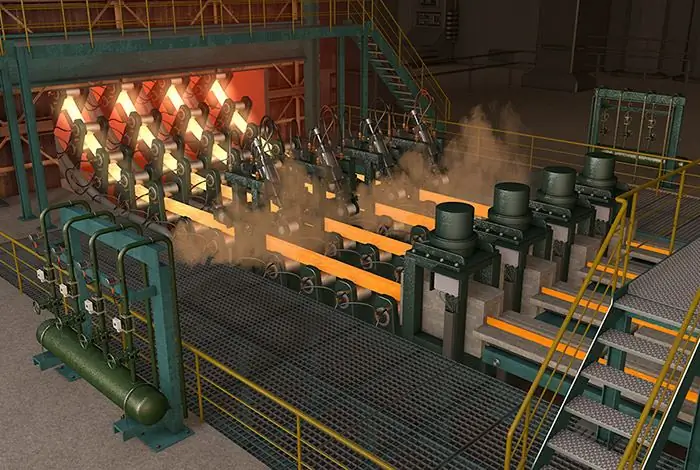
kora od ingota
Vrijedi napomenuti da se rad u vakuumu također smatra obećavajućom metodom livenja. Jedna jedinica može izvršitisipanje kroz nekoliko kalupa odjednom. Dakle, broj streamova jedne instalacije može doseći i do osam.
Rad hladnjaka hladnog sjemena se koristi za formiranje dna kože ingota. Ingot će izaći iz kalupa pod uticajem semena, koje se uvlači u sekundarnu zonu hlađenja (SCZ). U sredini gredice, čelik će i dalje biti u tečnom stanju. Ovdje je važno napomenuti da, prema zahtjevima tehnologije livenja čelika, debljina opne mora biti najmanje 25 mm u trenutku izlaska iz kalupa. Da bi se ispunili ovi zahtjevi, potrebno je odabrati pravi protok materijala.
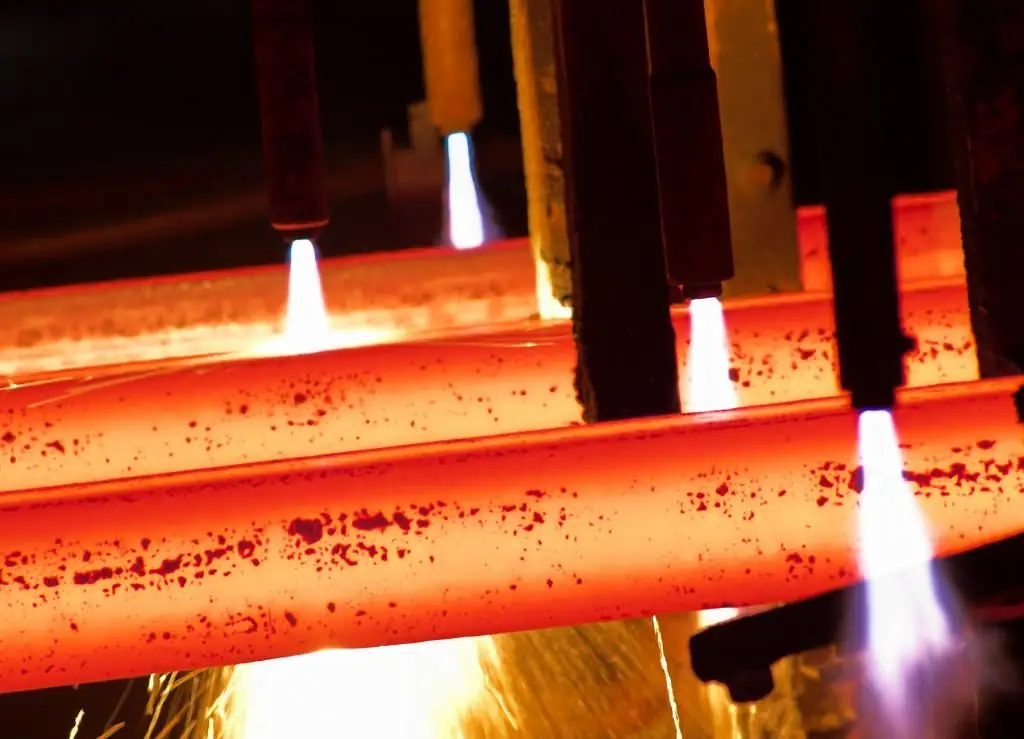
Karakteristike procesa ugradnje i livenja
Tehnološke karakteristike su otprilike sljedeće. Ako je presjek ingota 160x900 mm, tada bi njegova brzina trebala biti od 0,6 do 0,9 m/min. Ako je poprečni presjek 180x1000 mm, tada se brzina smanjuje na 0,55-0,85 m/min. Najveći indikator brzine je potreban za poprečni presjek ingota kvadratnog tipa 200x200 mm - 0,8-1,2 m/min.
Na osnovu gore navedenih pokazatelja možemo zaključiti da je prosječna brzina livenja jednog pramena upotrebom tehnologije kontinuiranog livenja 44,2 t/h. Ako prekoračite optimalnu brzinu, tada će se centralna poroznost povećati.
Dalje, vrijedi napomenuti da na stabilnost odljevka i kvalitet samog proizvoda utiče temperatura metala. Empirijski je utvrđeno da na temperaturi većoj od 1560 stepeniCelzijusova površina ingota često je prekrivena pukotinama. Ako je temperatura niža od naznačene, staklo će često biti zategnuto. Tako je utvrđeno da bi optimalna temperatura za metodu kontinuiranog livenja čelika bila 1540-1560 stepeni Celzijusa. Za održavanje ovog indikatora, temperatura grijanja peći prije puštanja treba biti u rasponu od 1630-1650 stepeni.
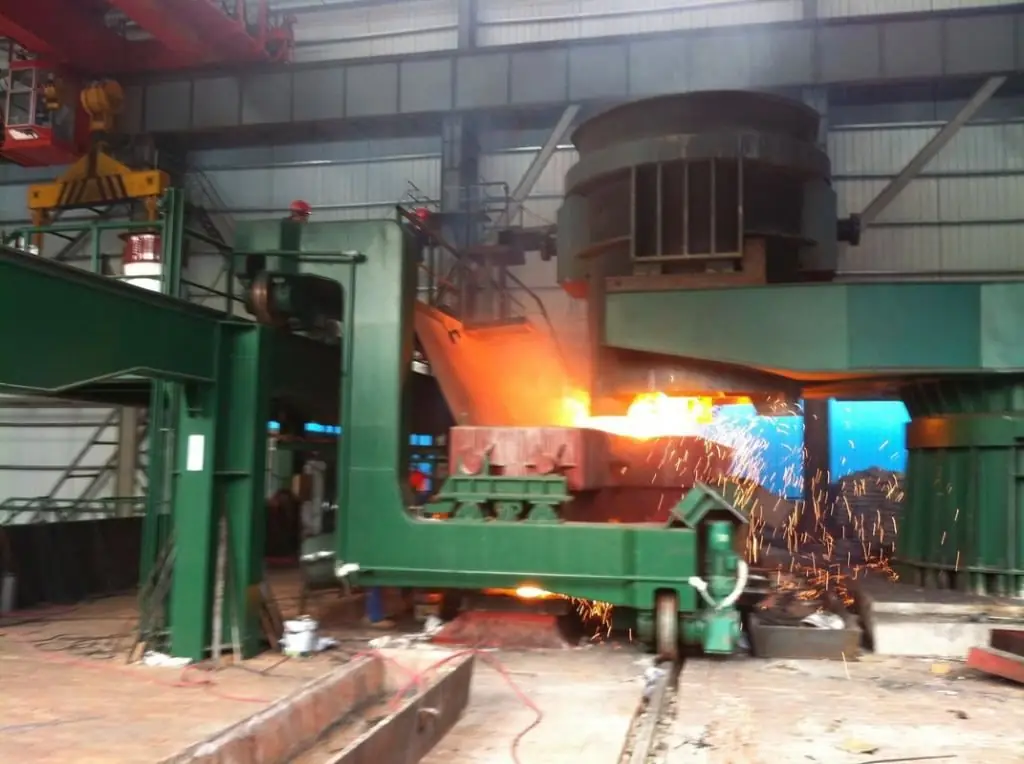
Sekundarna zona hlađenja
U ovoj sekciji najintenzivnije i najdirektnije hlađenje ingota se vrši uz pomoć vode koja dolazi iz raspršivača. Postoji poseban sistem praznog hoda, a ne pogonskih valjaka. Njihova rotacija sprečava savijanje ili savijanje ingota. Zbog intenzivnog hlađenja u ovoj zoni, zidovi ingota će se brzo povećati u debljini, a kristalizacija će se proširiti u dubinu. Brzinu izvlačenja ingota i stepen njegovog hlađenja treba odabrati tako da u trenutku kada ingot uđe u vučne valjke bude već potpuno čvrst.
Koje su prednosti kontinuiranog livenja
Pošto je ova metoda livenja čelika zamenila metodu izlivanja u kalupe, vredi uporediti sa ovom metodom. Općenito, vrijedi istaknuti sljedeće prednosti: veća produktivnost, smanjeni troškovi i smanjeni radni intenzitet procesa. Zbog konstantnog formiranja ingota, šupljina za skupljanje se prenosi na rep, za razliku od kalupa za ingote, gdje je svaki ingot imao svoju šupljinu. Zbog toga se značajno povećava procenat prinosa odgovarajućeg metala. UNRS vam omogućava da dobijeteradni komad raznih oblika, od malog kvadrata 40x40 mm do pravokutnika 250x1000 mm. Korištenje strojeva za kontinuirano lijevanje omogućilo je potpuno napuštanje mlinova za nabijanje. Time je značajno smanjen trošak procesa proizvodnje, a time i cijena na tržištu. Osim toga, proces metalurške obrade je pojednostavljen.
Nedostaci
Uprkos mogućnosti visoke mehanizacije i automatizacije procesa, visokom procentu dobrih ingota i drugim gore opisanim prednostima, ova metoda ima i neke negativne strane. Nedostaci čelika za kontinuirano lijevanje su sljedeći.
Prvo, ne postoji mogućnost proizvodnje ingota složene konfiguracije. Drugo, raspon ingota i praznina je prilično ograničen. Prilično je teško pretvoriti mašine u prelivanje sirovina druge marke, što može povećati konačnu cijenu proizvoda druge marke ako se proizvodi u istom pogonu. Neki tipovi čelika, na primjer oni koji ključaju, uopće se ne mogu napraviti ovom metodom.
Posljednji nedostatak metode kontinuiranog livenja čelika je vrlo značajan. To je mogući kvar opreme. Neuspjeh UNRS-a će dovesti do velikih gubitaka u performansama. Što je duže potrebno za popravku, gubici će rasti.
Preporučuje se:
Profesija blagajnik: uslovi rada, neophodna edukacija, dužnosti, prednosti i mane posla
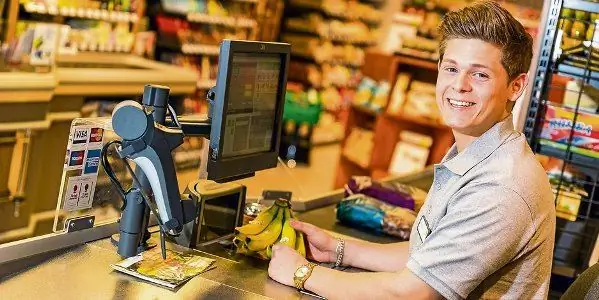
Svakoj kompaniji koja prima uplate od kupaca potreban je blagajnik. Upravo s ovim stručnjakom moraju imati posla posjetioci trgovačkih centara i ugostiteljskih objekata, kao i klijenti banaka i drugih organizacija. Nije iznenađujuće da je zanimanje blagajnika prilično traženo među potencijalnim poslodavcima. Ona privlači kandidate sa niskim zahtjevima koji se odnose na poziciju
Indikatori bez odlaganja i precrtavanja: vrste, princip rada, prednosti i nedostaci primjene, stručni savjeti
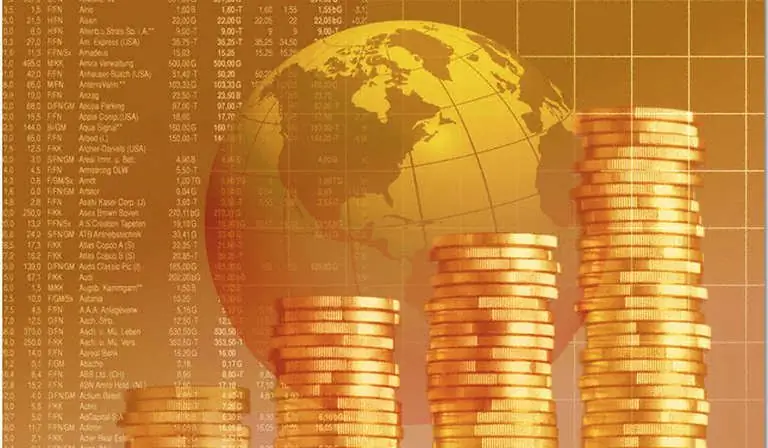
Postoji širok izbor različitih alata u trgovanju: grafičke konstrukcije, tehnički indikatori, automatizirani programi, trgovački signali i još mnogo toga. Da biste ih uspješno primijenili u trgovanju, morate razumjeti kako funkcioniraju. Indikatori bez odlaganja i ponovnog crtanja posebno su popularni kod trgovaca
Visoka štampa je Tehnologija visoke štampe, moderne faze razvoja, neophodna oprema, prednosti i mane ove vrste štampe
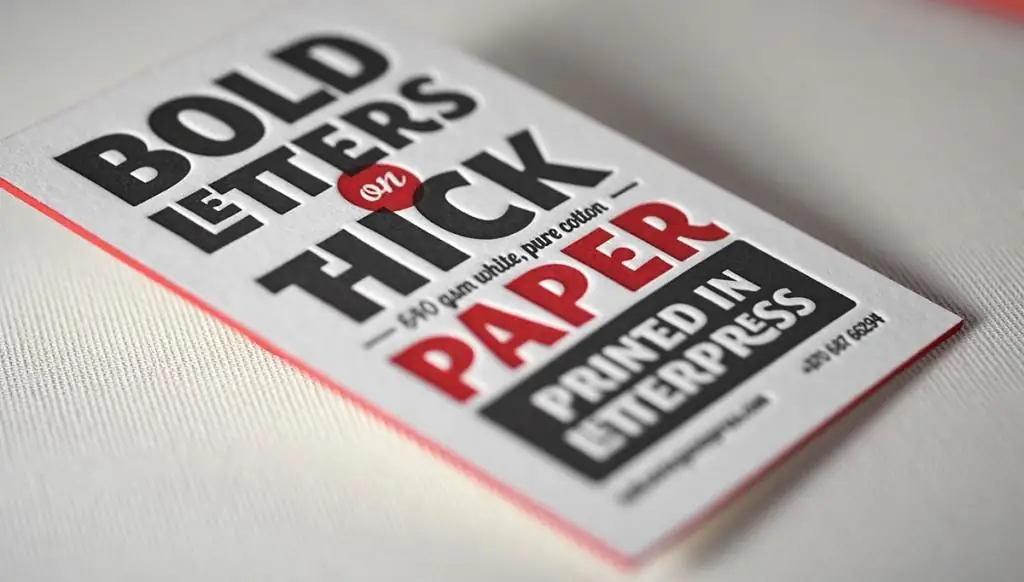
Visoka štampa je jedna od tipičnih metoda primjene informacija korištenjem reljefne matrice. Elementi koji strše prekriveni su bojom u obliku paste, a zatim pritisnuti na papir. Tako se umnožavaju razne masovne periodike, priručnike, knjige i novine
Princip rada dizel motora: karakteristike, prednosti i nedostaci
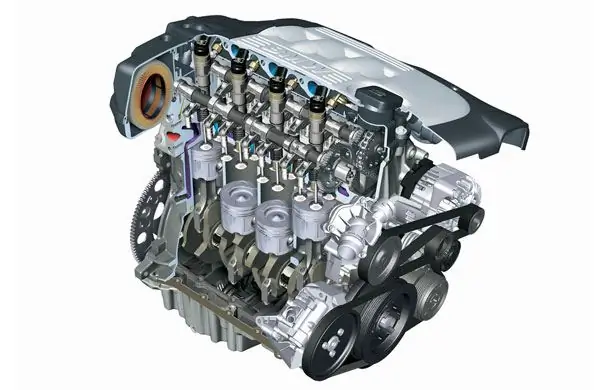
Dizel automobili na našim cestama nisu neuobičajeni. U zemljama zapadne Evrope oni su u većini. Dizel motori imaju niz prednosti u odnosu na benzinske. Ali u isto vrijeme, postoje i neki nedostaci. Šta je ovo motor, koji je dizel uređaj i princip rada? Razmotrite u našem današnjem članku
Diesel podmornice: istorijat stvaranja, projekti brodova, princip rada, prednosti, nedostaci i faze razvoja
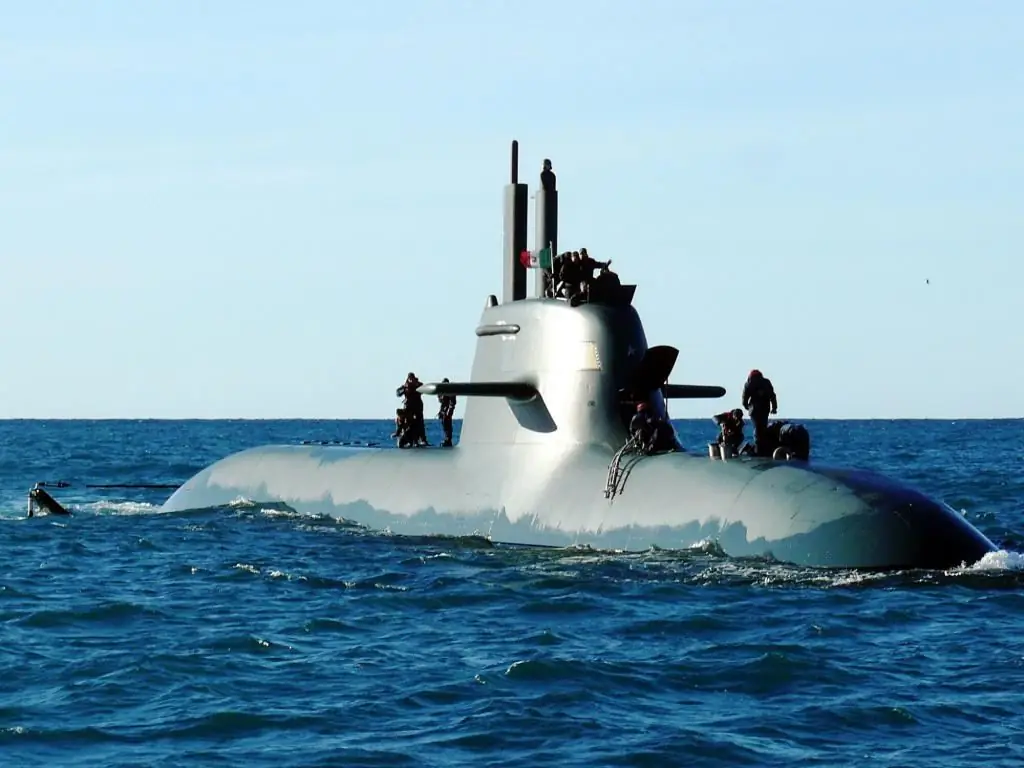
Ideja o stvaranju podmornice koja se kreće pod vodom, zapravo prototipa podmornice (u daljem tekstu podmornica), nastala je mnogo prije njihovog stvarnog pojavljivanja u 18. stoljeću. Nema tačnih opisa podvodnih vozila u brojnim legendama, kao ni u renesansnom geniju Leonardu da Vinčiju